OPTICAL SURFACE QUALITY EVALUATION ACC. TO MIL-PRF-13830B
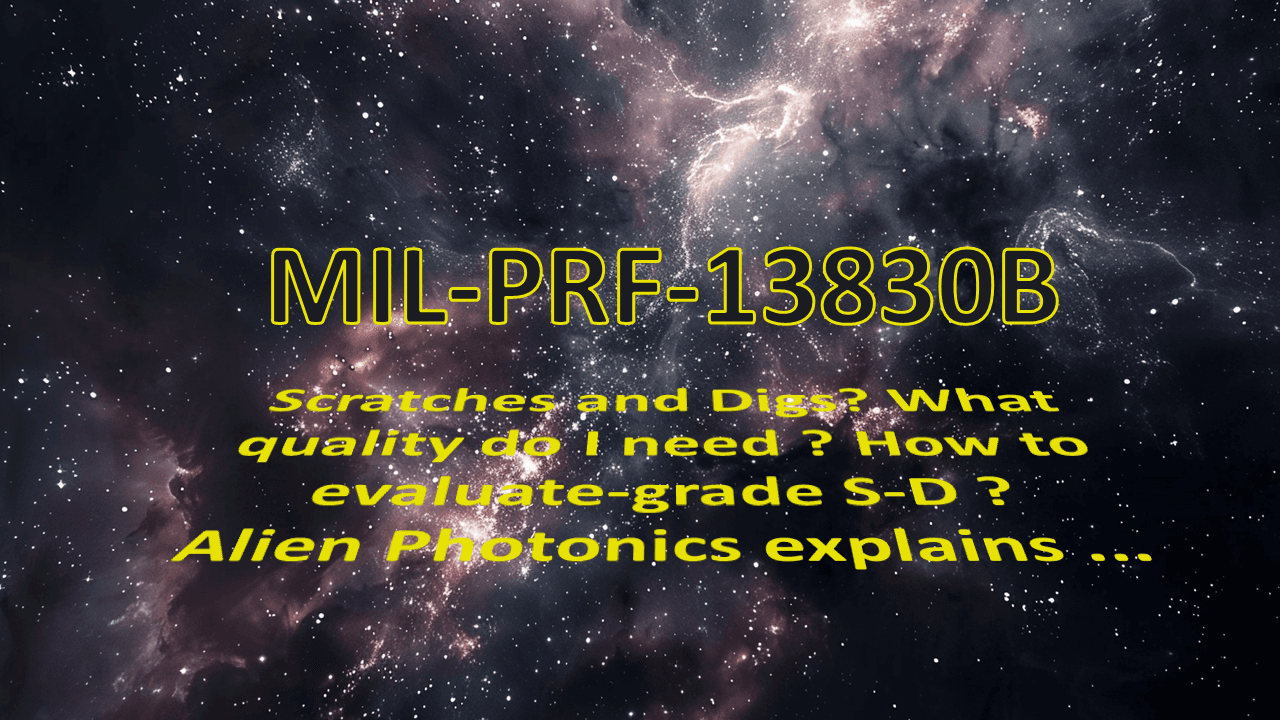
MIL-PRF-13830B introduction
MIL-PRF-13830B is probably the most widely adopted and accepted optical surface quality standard on Earth. While sometimes ISO10110-7 (2017) is encouraged to be used, still most of optical components companies prefer time-tested MIL standard. Scratch and dig standard is quite subjective, because it involves visual observation of an element comparing it to standard.
Scratch (Scr, S) – any tearing or marking on(in) the optical surface
- Scratch is measured in terms of its’ width and is classified within different width-based grades. E.g. 60-40 S-D specification, means that maximum width of allowed scratch is 60 μm.
- Inspection of scratch is evaluated visually under controlled illumination. Most popular method is direct comparison to reference patterns (standard etalons)
- According to section 3.5.2, the total sum of length of all maximum allowed size scratches (on each surface!) shall not exceed 1/4 (quarter) of the diameter of round optical component's clear aperture. If you are interested in details for non-circular, prisms, etc. please check full standard.
- Coating scratches which do not penetrate the glass surface (on coating only), are characterized the same way as with glass surface. Quality assurance specialist shoud evaluate substrate and coating scratches separately.
Dig (D) – small rough pit or localized spot on(in) the optical surface.
- Inspection of dig. Similarly to scratch, dig is evaluated visually, under controlled light. Most popular method is direct comparison to reference patterns (standard etalons). E.g. 60-40 S-D means that max allowable dig diameter is 400 μm (0.4 mm).
- Dig is measured by its diameter. If it is not “round”, but rather elliptical, then quality assurance specialist has to take into account both diameters.
- The total sum of the diameters of all the digs shall not be more than twice the diameter size of the maximum size dig specified per 20 mm. Digs less than 2.5 μm shall be ignored.
- Bubbles and inclusions in glass should be treated as digs.
Scratch-dig (Scr-dig, S-D) grading - summary table
Class | Quality | Typical Applications |
---|---|---|
0-0 S-D | Perfect | Deep UV laser systems |
5-3 S-D | Near-Perfect | Deep UV laser systems |
10-5 S-D | Very high | Deep UV or high-power laser systems |
20-10 S-D | High | High power laser systems |
40-20 S-D | Medium | Medium power or IR laser systems. Standard quality for scientific research applications. |
60-40 S-D | Low | Low power optical devices or imaging applications, IR laser systems |
80-50 S-D | Very low | Low power optical devices or imaging applications, IR laser systems |
120-80 S-D | Very low | Low power optical devices or imaging applications, IR laser systems |
Testing sequence according to MIL-PRF-13830B
Inspection of mechanical dimensions and X-ray test to check for radioactive materials.
- Optical components dimensions (width, length, diameter, thickness, etc.) are tested according to procedures, or in case of custom optical component to specific drawing.
- While X-ray test checks if there are any detectable radioactive materials. If radioactivity is detected, all glass from the lot must be rejected.
Surface quality evaluation with one of two methods:
since the evaluation is already quite subjective. It is typically done in black background using
- 40W incandescent light source to illuminate optical component from the back side
- 15W cold white fluorescent light from ~3 inch distance from optical component.
However, even when using these lighting setups not all defects are visible, upon request for defect-sensitive applications Alien Photonics perform high power light measurements.
Other tests
Once surface quality testing is conducted, the other tests - temperature, humidity, centricity, etc. are done.
Looking for specific testing of your optics? Check Alien Photonics metrology page.