HIGH QUALITY OPTICAL COMPONENTS FOR LASER MICROMACHINING
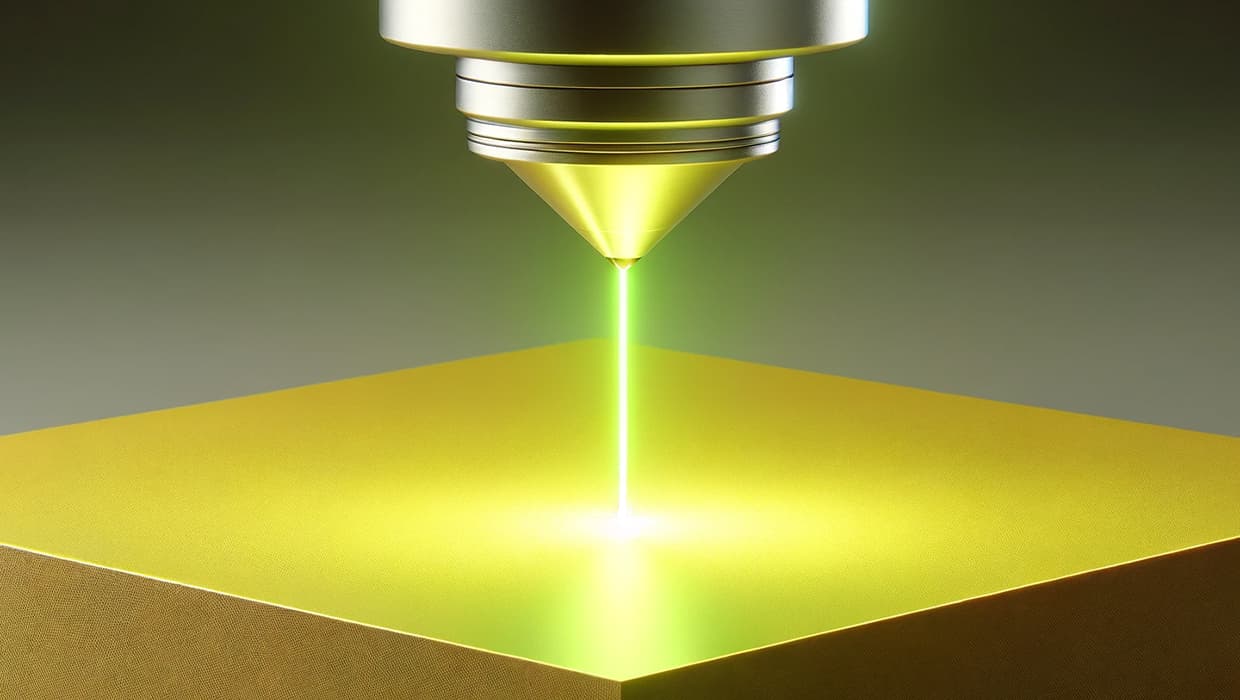
Lenses for laser micromachining - spherical, cylindrical, aspherical or conical (axicons)?
Whichever laser source you use - Fiber laser to cut metals, CO2 in textile, synthetic and other materials, maybe solid state (Nd:YAG, Nd:YVO₄, Er:YAG, Yb:YAG, …) or other laser type – optical components are the key building block in laser micromachining systems. Some types of Alien Photonics lenses are used for laser micromachining with few of examples can be found bellow:
- Lenses focus the laser beam to engrave or sometimes even cut designs and ornaments on precious metals and gemstones in jewelry production.
- Furthermore, lenses focus the laser beam, concentrating the energy and thus micro-wielding tiny components becomes available, usually wielding small electronics components (as well as jewelry production mentioned above).
- During the LASIK (Laser-assisted in situ keratomileusis, or laser eye surgery or laser vision correction) lenses are used to focus the laser beam to reshape the cornea with maximal precision.
Most popular focusing (converging) lenses for micromachining:
Criteria | Spherica | Cylindrical | Aspherical | Axicon |
---|---|---|---|---|
Product link | Spherical | Cylindrical | Aspherical | Axicon |
Function | Focus light in all directions equally. | Focus light in one direction. | Correct spherical aberrations (more precise focus). | Transform laser beam to ring-shape or create Bessel beams. |
General applications | Cutting, drilling, R&D. | Engraving, material processing along a line. | Hug precision micromachining. | Drilling holes with reduced taper. |
Challenges | Spherical aberrations. | Limited to linear applications, astigmatism. | Higher cost, complex. | Very limited number of applications. |
Polarizers for laser micromachining: Waveplates, TFP polarizers and PBS cubes
Polarizers are another Alien Photonics product which are widely adopted in micromachining applications, especially:
- During micro-processing of birefringent materials (materials which have different refractive indices along different axis) polarizers can be adjusted to match the optical axis of the material. In this way ensuring efficient and precise machining.
- In micro-drilling, especially glass, polarizers can be adjusted and can lead to more circular holes, smoother sidewalls.
- Polarizers in precision micromachining can be fine tunned to reduce (unwanted) side effects, such as burr formation or heat-induced damage around drilled holes.
Criteria | Polarizers (TFP and PBS) | Waveplates |
---|---|---|
Function | Filter (separate) light based on polarization. | Change/Alter polarization state without filtering/blocking it. |
General Applications | Precision drilling birefringent materials, enhancing quality. | Maintaining beam energy in specific applications. |
Flexibility | Typically used to block one polarization and transmit another. | More precise control possible over the polarization state. |
High reflection and partial reflection mirrors for laser micromachining applications
Laser mirrors for micromachining
Laser line mirrors (Nd:YAG, Yb:YAG, Ti:Sapphire), dual band mirrors (Nd:YAG DBHR, Yb:YAG DBHR, Ti:Sapphire DBHR), metallic mirrors (Au, Ag, Al) and custom mirrors (Single band, Dual-band, Broadband) from Alien Photonics are produced while keeping in mind the requirements for most common applications:
- Laser mirrors to direct the laser beam in CNC (Computerized Numerical Control) machines (CNC cutters), when cutting materials like acrylic or wood.
- Laser mirrors to guide laser beam in barcode scanning devices quickly. - Custom laser line mirrors for micromachining research experiments.
Laser micromachining beamsplitters (partial reflectors)
And finally, Beamsplitters. There are quite a few places in laser micromachining setups, where these optical components can play a crucial role. Here is couple of them:
- Multi-track wielding, e.g. assembling optical sensors, or other micro(electronic) devices, beamsplitters helps to create multiple wielding points simultaneously. This solution, not just speeds up the production, but also ensures uniformity, repeatability and consistency in the wielding quality.
- Array micro-drilling, similarly during the production of nozzle plates beam splitters can be used to create multiple hole drilling set-up.
Comparison of dielectric, metallic mirrors and dielectric partial reflectors for micromachining applications
Criteria | Dielectric Mirrors | Metallic Mirrors | Partial Reflectors |
---|---|---|---|
Function | Reflects specific laser wavelength (range). | Reflects specific laser wavelength (range). | Separates beam into two beams. |
Reflection | E-beam (EBE) >99.0%-99.7%; IBS >99.0%-99.95% | Typically, more than 90~96% over the range. | Based on design R-T 50%-50%, 70%-30%, or custom 80%-20% |
Laser Induced Damage Threshold (LIDT) | Highest. | Lowest. | Varies. Generally lower than dielectric mirrors. |
Durability and Lifetime | Durable, depends on coating technology. Sputtering – higher durability, evaporation - lower durability, more sensitive, but still typically better than metallic. | Lower durability, especially with higher intensity and harsh environments. Upon request protective coating can be applied to minimize effects. | Same as dielectric mirrors, but might be more sensitive to laser damage, since are used in Transmission configuration. |
General applications | Precision laser micromachining systems. | Less expensive, table-top, simpler micromachining systems. | Multi-beam processing systems. |
Challenges | Cost, characteristics suitable for single wavelength. | If not protected, susceptible to degradation. Not suitable for high powers. | Deviation of split ratio, precision alignment. |
Looking for optical component not mentioned in this article? Check our Laser optics, Polarizers and Lenses product groups. Still having trouble finding the right one? Contact us and Alien Photonics will help you to choose perfect component for your laser micro-machining applications.